The application of nitrogen/argon-protected jet mills in the ultrafine grinding of neodymium iron boron (NdFeB) materials. NdFeB magnets are known for their high magnetic energy and strength. They are crucial in many industries, including electronics and renewable energy. Processing them into ultrafine powders is tough. This is because they are highly reactive, pyrophoric, and prone to oxidation. Traditional grinding methods often can’t meet the high purity and uniformity needed for advanced uses. This includes additive manufacturing and high-performance magnets. Jet milling, particularly under inert gas environments (nitrogen or argon), has emerged as a superior solution. This article looks at the technical principles and benefits of inert gas-protected jet mills in NdFeB processing. It also explores their industrial uses.
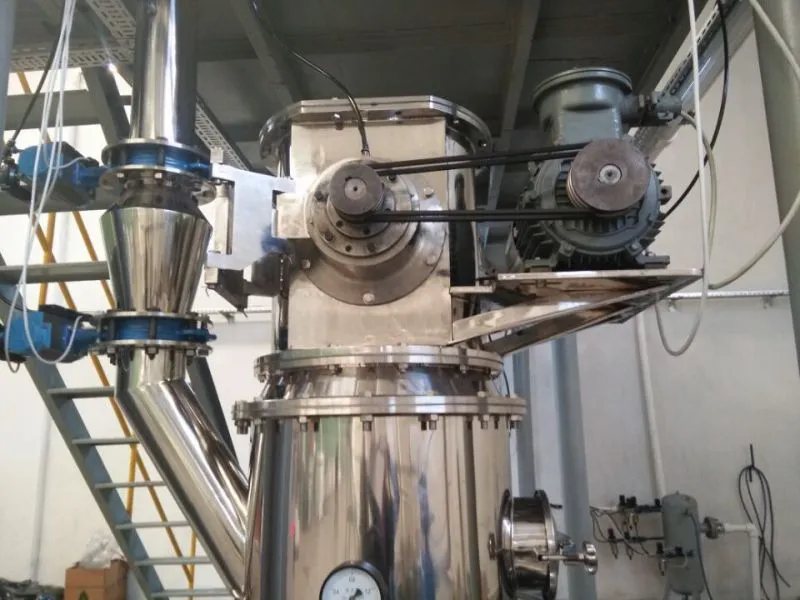
Challenges in NdFeB Powder Processing
Material Reactivity and Oxidation Risks
NdFeB alloys have rare-earth elements, like neodymium. These elements can quickly oxidize in air. This oxidation causes weaker magnetic properties and can even pose ignition risks during milling. Conventional grinding generates heat and friction, exacerbating oxidation and contamination.
Particle Size and Morphology Requirements
Advanced applications demand powders with:
- Ultrafine particle sizes (D90 < 3 µm) for uniform sintering .
- Narrow size distribution to ensure consistent packing density.
- Spherical or equiaxed morphology for improved flowability in 3D printing .
Jet Milling Technology: Principles and Adaptations for Inert Gas Use
Jet Mill Working Mechanism
Jet mills utilize high-velocity gas streams (compressed air, nitrogen, or argon) to achieve particle size reduction through interparticle collision and attrition. Key components include:
- Grinding Chamber: Particles are accelerated to supersonic speeds (up to 300 m/s) via converging-diverging nozzles .
- Classification System: Integrated classifiers (e.g., centrifugal or inertial) separate fine particles from oversize material, ensuring precise size control .
Inert Gas Integration
Replacing air with nitrogen or argon addresses NdFeB’s reactivity:
- Oxygen Exclusion: Inert gases create an oxygen-free environment (<10 ppm O₂), preventing oxidation during milling .
- Cooling Effect: Gas expansion absorbs heat, maintaining low temperatures (e.g., -40°C in cryogenic systems) to avoid thermal degradation 7.
- Explosion Prevention: Mitigates risks of dust explosions common in reactive metal processing .
Gas Selection Criteria:
- Nitrogen: Cost-effective, widely available, suitable for most NdFeB grades.
- Argon: Higher inertness, preferred for ultra-high-purity applications (e.g., aerospace components) .
Equipment Design and Operational Best Practices
Jet Mill Configurations for Inert Gas Use
- Closed-Loop Systems: Recirculate inert gas to minimize consumption, with oxygen sensors for real-time monitoring .
- Material-Specific Nozzle Designs: Optimized nozzle geometries (e.g., Laval nozzles) enhance particle acceleration and collision efficiency .
- Cryogenic Adaptations: Combine liquid nitrogen cooling with jet milling for submicron powders (D50 < 1 µm) .
Key Operational Parameters
- Gas Pressure: Higher pressures (6–10 bar) increase kinetic energy, improving grinding efficiency but requiring robust chamber designs .
- Feed Rate Control: Consistent feeding prevents overloading, ensuring uniform particle size distribution .
- Temperature Management: Thermocouples and gas chillers maintain temperatures below NdFeB’s oxidation threshold (~150°C) .
Case Studies: Industrial Applications
High-Performance Magnet Production
A leading NdFeB manufacturer achieved D90 = 2.5 µm powders using a nitrogen-protected jet mill (JetMill Pilot, 0.5–30 kg/hr capacity), reducing oxygen content by 98% compared to air-milled powders .
Additive Manufacturing of Magnetic Components
A 3D printing firm utilized argon-protected milling to produce spherical NdFeB powders (D50 = 15 µm) for binder jetting, achieving >99% density in sintered parts .
Advantages of Inert Gas Jet Milling for NdFeB
- Enhanced Purity: Oxygen content <100 ppm, critical for high-coercivity magnets .
- Superior Particle Control: Adjustable classifiers enable tailored size distributions (0.1–20 µm) .
- Safety Compliance: Eliminates explosion risks, aligning with ATEX and OSHA standards .
Challenges and Mitigation Strategies
- Gas Cost Management: Closed-loop systems and on-site nitrogen generators reduce operational expenses .
- Contamination Risks: Hardened stainless steel or ceramic-lined chambers prevent metallic impurities .
Nitrogen and argon-protected jet mills represent a transformative approach to NdFeB powder processing, balancing precision, safety, and material integrity. As industries demand higher-performance magnets and sustainable manufacturing practices, adopting inert gas jet milling will remain pivotal.