Ceramic powders are the fundamental “cells” in ceramic material R&D and production. Ceramic powder preparation process directly affects the performance and quality of final ceramic products. Advanced technologies enable the synthesis of nano-scale ceramic powders. Traditional raw materials are also being processed with greater precision. These innovations continue to evolve.
They are pushing the ceramic industry to new heights.
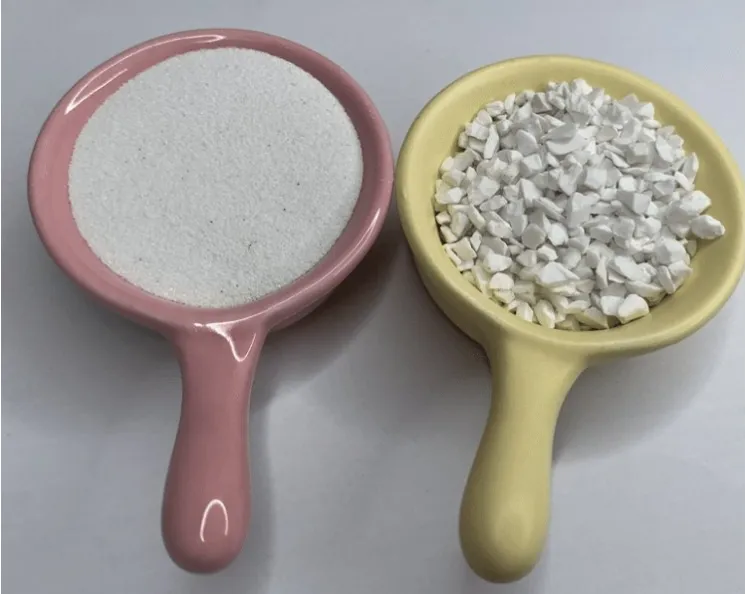
Traditional powder preparation process
The method of mechanical size reduction is widely used in the ceramic industry. Crushing ceramic raw materials improves the quality of formed bodies. It increases density and aids physical and chemical reactions during sintering. It also helps lower the firing temperature.
Jaw Crusher
Jaw crushers are commonly used for coarse crushing in ceramic production. They are mainly for pre-processing large lumps. The structure is simple, and operation is easy. They offer high output efficiency. However, the crushing ratio is small, about 4. Feed size is usually large, so output is coarse. The particle size adjustment range is also limited.
Roller Crusher
Roll crushers have high crushing efficiency and a large ratio (over 60). They produce fine particles, often reaching 44 μm. However, high-speed grinding of hard materials causes heavy wear. This introduces more iron into the powder. It affects raw material purity, requiring iron removal later. Due to their design, particle size distribution is narrow. They are only suitable for materials needing specific size ranges.
Wheel Roller
Pan mills are commonly used in ceramic production for crushing and mixing materials.
Raw materials are ground between the pan and rollers. Grinding occurs by sliding and the roller’s weight. Heavier and larger rollers give stronger crushing force. Stone rollers and pans help prevent iron contamination. Pan mills have a large crushing ratio, about 10. Processed materials have a defined particle size range. Finer particle requirements reduce production capacity. Wet milling can also be used in pan mills.
Ball mill
Ball mills are widely used in industry for fine grinding and mixing. To ensure purity, ceramic or polymer liners are used. Various ceramic balls serve as grinding media. In wet milling, the medium splits cracks on material surfaces. Intermittent wet milling is more efficient than dry milling. Wet milling can produce powders down to a few microns. Ball mill speed affects grinding efficiency. Speed controls the movement of the ball within the drum.
Too fast: the balls stick to the wall and the grinding effect is lost.
Too slow: the balls fall quickly and the crushing force is small.
Appropriate speed: the balls fall from a height to maximize the impact force.
This gives the highest grinding efficiency. The critical speed depends on the drum diameter. The larger the diameter, the lower the critical speed.
Air jet mill
Air jet mill or air jet pulverizer can obtain powder of 0.1~0.5 µm. The working principle is: compressed air passes through the nozzle to form a high-speed airflow in the space, so that the powders collide with each other in the high-speed airflow to achieve the purpose of crushing. The powder crushed by the airflow pulverizer has a uniform particle size distribution, high crushing efficiency, can ensure purity, and can be crushed in a protective gas.
Vibration mill
Vibration mill has a very high crushing efficiency. Vibration mill uses grinding balls to make high-frequency vibrations in the mill to crush raw materials. In addition to intense circulation, the grinding balls also have intense self-rotation motion. It has a great grinding effect on the raw materials. The powder particle size can reach 1 μm during wet grinding.
Preparation of ceramic powder by solid phase method
The solid phase method uses various solid reactions between solid substances to produce powders. Common solid reactions in the preparation of ceramic powder raw materials include chemical reactions, thermal decomposition reactions and oxide reduction reactions. However, these reactions often occur simultaneously in the actual process. The powder prepared by the solid phase method cannot be used directly as a raw material and needs to be further crushed.
Chemical reaction:
- Barium Titanate: BaCO3+TiO 2=BaTiO 3+CO2
- Spinel: Al 2O3+MgO=MgAl 2O4
- Mullite: 3Al 2O3+2SiO2=3Al 2O3-2SiO2
Thermal decomposition reaction:
Many high-purity oxide powders can be prepared by heating the sulfates and nitrates of the corresponding metals and thermally decomposing them to obtain powders with excellent properties. For example, aluminum ammonium sulfate can be heated in air to obtain aluminum oxide powder with excellent properties.
Oxide reduction reaction:
Silicon carbide and silicon nitride are very important advanced engineering ceramic materials. For the preparation of raw material powders of these two ceramic materials, the oxide reduction method is often used in industry.
Silicon Carbide: SiO2+3C=SiC+2CO
Silicon: SiO2+2C=Si+2CO
Silicon Nitride: 3SiO2+6C +4N 2=2Si3N4+6CO
Preparation of ceramic powder by liquid phase method
Ultrafine powders produced by liquid phase method have been widely used in the manufacture of advanced ceramic materials. The main advantage of liquid phase method for preparing ceramic powders is that it can better control the chemical composition of the powder, obtain a well-mixed multi-component composite powder at a higher (ionic) level, and facilitate the addition of trace components.
Preparation of ceramic powder by gas phase method
The raw materials are heated by electric arc or plasma until they are gasified, and then rapidly cooled under the condition of a large temperature gradient between the heating source and the environment to condense into powder particles. The particle size can reach 5~100nm. It is suitable for the preparation of single-phase oxides, composite oxides, carbides and metal powders.
Conclusion
The preparation process of ceramic powder materials continues to evolve through ongoing technological advancements. From traditional methods rooted in experience to the adoption of cutting-edge technologies, progress has been steady. These developments not only improve powder quality but also expand the application scope of ceramic materials. They bring new vitality to the sustainable development of the ceramic industry. Looking ahead, as material science and processing technology deeply integrate, the preparation of ceramic powders is expected to achieve greater breakthroughs. This will lead the ceramic industry toward an even brighter future.
Epic powder
Epic Powder, 20+ years of work experience in the ultrafine powder industry. Actively promote the future development of ultra-fine powder, focusing on crushing,grinding,classifying and modification process of ultra-fine powder. Contact us for a free consultation and customized solutions! Our expert team is dedicated to providing high-quality products and services to maximize the value of your powder processing. Epic Powder—Your Trusted Powder Processing Expert !